3.The Second Generation of Rare Earth Permanent-Magnet Alloys: Advancements and Properties
This chapter discusses the second generation rare earth Magnets alloy, the 2:17 type rare earth cobalt permanent magnetic alloy (\(RE_2Co_{17}\)).
\(Sm(Co, Cu, Fe, Zr)_{7.4}\) alloy of high coercivity is a precipitated hardening permanent magnetic alloy. This alloy has the highest Curie temperature of \(T_C = 850^{\circ}C\). Its intrinsic coercivity, magnetic induction intensity and theoretical magnetic energy product are higher than those of \(RECo_5\). The structure of this type of alloy: in the center is \(Sm_2(Co, Cu, Fe, Zr)_{17}\) of about 50nm. The boundary phase is comprised of \(Sm(Co, Cu, Fe, Zr)_5\) with a thickness about 10nm surrounding the main phase. This is called a cystiform structure. The coercivity of the 2:17 type alloy does not rely on the size of crystal grain, rather on the microstructure between two phases. These two phases are the 2:17 phase and the 1:5 phase. The domain of 2:17 phase is pinned by the 1:5 phase when magnetization and anti - magnetization, due to the difference in domain between the 2:17 phase and 1:5 phase. Thus, the alloy possesses very high coercivity. The key for obtaining high coercivity depends on the heat treatment technique, which generally adopts solid solution treatment, isothermal ageing treatment, etc.
This chapter expatiates in emphasis on observation and research of high coercivity \(Sm(Co, Cu, Fe, Zr)_{7.4}\) alloy using JEM - 1000 HVEM, especially the in situ observation on precipitation, growth and growth velocity of cystiform structure at continual rising temperature from room temperature to 950°C. The analysis and deep research were carried out on the driving force and resistance of phase transformation process, phase transformation dynamics, coercivity mechanism of cystiform structure broken under long term high temperature ageing, diffusion type continual phase transformation and new opinion on enhancing metastable phase transition to phase. Research was made on zirconium in \(Sm(Co, Cu, Fe, Zr)_{7.4}\) alloy to enhance coercivity, heighten solubility of Sm in the alloy, improve square degree of demagnetization curve through nuclear physics method. Iron atom was promoted to enter into \(Co_3\) site from \(Co_1\) site in 2:17 phase and thus to raise uniaxial anisotropy of alloy. These two points benefit the enhancement of the coercivity of this alloy.
This chapter also researches the magnetism of high coercivity \(Sm(Co, Cu, Fe, Zr)_{7.4}\) permanent magnetic alloy from 1.5K to 523K, measured the magnetism of the alloy after spinning and re - orientation at 1.5K and magnetism at 1.5K with changing temperature.
Phase Precipitation, High-Temperature Phase Transformation, and Magnetism of High-Coercivity Sm(Co, Cu, Fe, Zr)₇.₄
The Curie temperature and saturation magnetization intensity of \(Sm_2Co_{17}\) are both higher than \(RECo_5\) among the rare earth Co - intermetallic compounds, and it has been widely used in industry, agriculture, and national defense and transportation areas for more than twenty years. Among the \(Sm_2Co_{17}\) type permanent magnetic alloys the most excellent in magnetic performance is Sm - Co - Cu - Fe - M series, where M are \(Zr\), \(Hf\), \(Ti\), \(Ni\), \(Mn\), etc. However, \(Sm(Co, Cu, Fe, Zr)_{7.0 - 8.0}\) is the best one in magnetic performance among all the \(Sm_2Co_{17}\) permanent magnetic alloys. \(Sm_2Co_{17}\) alloys can be divided into three kinds in accordance with their zirconium content. The first kind has a higher magnetic - energy product and low coercivity, and its magnetic performance is: \((BH)_{max}=175 - 251kJ/m^3\). It has a better quadrate degree in its demagnetization curve. The second kind has super high coercivity, and its coercivity \(_{m}H_c = 1990 - 2388\) kA/m, \((BH)_{max}= 190 - 223\) kJ/m². The third kind is in between, which is called \(Sm_2Co_{17}\) permanent - magnet alloy with high coercivity that \(_{m}H_c = 796 - 1259\) kA/m, \(_{b}H_c = 636 - 716\)kA/m, \((BH)_{max}= 199 - 223kJ/m^2\). Its Curie temperature is \(840 - 870^{\circ}C\), magnetic induction temperature coefficient is \(- 0.02\%/^{\circ}C\). It can be used at the temperature among \(- 60 - 350^{\circ}C\), and is lower in the quantity of samarium and cobalt, so that it may be a potentially ideal permanent magnet alloy, of which the theoretical magnetic - energy product may reach \(525.4kJ/m^3\) (66 MGs·Oe). From the magnetic performance mentioned above, its actual magnetic - energy product is only a half of the theoretical value, thus it has to sacrifice some coercivity in order to enhance magnetic - energy product. How to enhance coercivity further at the same time to get high magnetic - energy product? For this purpose it is necessary to study coercivity theoretically (Zhou, 1990).
\(Sm(Co, Cu, Fe, Zr)_{7.4}\) with high coercivity is a kind of precipitation - hardening permanent magnet alloy with cellular microstructure. The coercivity of the alloy is determined by pinning from cellular structure to domain wall. What is the pinning center of domain wall? Are there some relationships between coercivity and the size and shape of the cellular structure, incompleteness of appearance and growth of cell, and coherency stress state of matrix phase and precipitated phase?
There are many approaches for studying coercivity. It is to study specimens with different coercivity using nuclear physical method and analyze the result with combining magnetism loop getting from magnetic measurement; another is to build a physical model to research relationships between coercivity and physical and geometrical parameters of the precipitated phase after mathematical treatment. The third is to observe at first, the microtexture of the alloy using HVEM and to measure magnetism parameters, and research the relationship between coercivity and geometrical parameter of microtexture and physical parameters of new phase after measuring coercivity.
Coercivity is a physical quantity being sensitive to microtexture. The relationship and interaction of microtexture and domain structure are the foundations for researching coercivity of permanent - magnet alloy. The scholars engaged with this study and scientists working on magnetics and metal physics have made a lot of excellent achievements. But the microtexture obtained by above experiments was observed at room temperature so that it lacks the integral and systemic understanding on the formation of phase (Zhou, 1990; Pan, Ma, Li, 1993; Pan, Zhao, 1988; Xiao, Zhang, Zhou, et al, 1982; Rothwarf, et al, 1982; Fidler, et al, 1982; Yu, 2003).
This study adopted a 1000kV HVEM for dynamic observation on alloy specimen at thermal state for a more accurate understanding on formation of various microtexture and associated with variation of coercivity in different states so that to judge the influence of microtexture of the alloy on coercivity further for purpose of studying coercivity and thus enhancing the coercivity.
Recent research work on \((Sm_{1 - x}Gd_x)(Co, Cu, Fe, Zr)_z\) indicates the temperature coefficient reaches zero when \(x = 0.55\). And \(z\) value affects the temperature coefficient as well. When \(z = 7.87\) the alloy has the lowest point at \(z\) value vs the temperature coefficient curve (Pan, 2011).
Specimen Preparation Process and Experimental Methods for Studying Sm(Co, Cu, Fe, Zr)₇.₄
Powder metallurgy was used to prepare \(Sm(Co, Cu, Fe, Zr)_{7.4}\) in the experiment. The chemical composition (mass fraction) was: 26%Sm, 51.4%Co, 15.8%Fe, 2.4%Zr and 4.4%Cu. The alloy with above composition was melted in vacuum induction furnace and molding in water - cooling copper mould. After the ingot obtained was crushed coarsely and pulverized to powder of about 5μm as the average granularity under the protection of toluene. The powder was oriented in magnetic field of 1.5T and formed in press machine. The formed roughcast was sintered at 1210°C and solid dissolved at 1155°C and then wind cooled to room temperature for use. The aging temperature was 850°C and 400°C. Then the specimen was ready for magnetism measurement using CL6 - 1 magnetic parameter instrument.
The preparation method of specimen for observation by electronic microscopic was as follows. First, solid resolving the alloy for 0.5h and quenching to room temperature. Then the specimen was sliced into lamellae with a thickness of 0.25mm at the direction perpendicular to c axis. At last, the film specimen was thinned and rinsed at ion - thinning machine.
Both static and dynamic observation of filmy specimen was proceed in JEM - 1000 HVEM with operation voltage 1000 kV in vacuum of \(2.5\times10^{-4}\)Pa and \(0.7\times10^{-5}\)Pa after adding liquid nitrogen. Ionic beam was 10μA. The specimen was inserted into the side inserted heating experiment dais of TEM - 1000 and was heated - up from room temperature to high temperature, held and videotaped in electronic microscope in dynamic observation. The change in microtexture of permanent - magnet alloy was observed directly in electronic microscope and relevant electronic diffraction diagram was made.
Magnetic Measurement Results of Sm(Co, Cu, Fe, Zr)₇.₄ Permanent Magnets
The specimen was measured magnetically using magnetic parameter measurement apparatus. The results of magnetic measurement was as follows: the magnetic remanence induction intensity \(B_r = 1.12\)T, intrinsic coercivity \(_{i}H_c = 1078\) kA/m, and maximum magnetic energy product \((BH)_{max}= 243.6\)kJ/m³. The demagnetization curve of the specimen is shown in Fig. 3.1, and the curve at rising temperature is shown in Fig. 3.2.
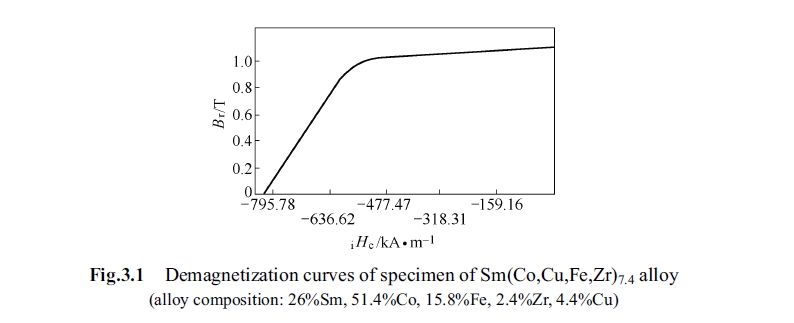
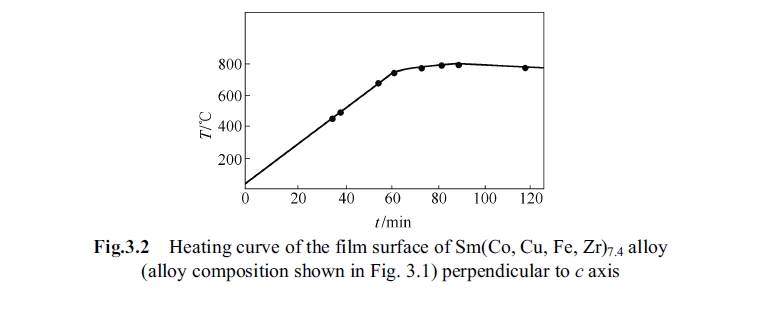
Microtexture Analysis of Sm(Co, Cu, Fe, Zr)₇.₄ Alloy at Room Temperaturee
After solid solution treatment and succedent aging treatment at below 850°C, microtexture of the alloy appeared in exiguous cellular at the state of high coercivity. The cell wall was 1:5 type phase, the inner - cell was 2:17 type phase, and the two type phases are coherent (Fig. 3.3). The diameter of cell is about 50nm and the thickness of cell wall was 5nm (Rothworf, 1982). The plane was vertical to c axis thus the cells was equal - axial. Fig. 3.4 shows the electronic diffraction pattern. Fig. 3.5 shows the microtexture at room temperature. Fig. 3.6 shows electron micrograph at room temperature. Fig. 3.7 shows the relationship between diameter of cell and coercivity of 2:17 type alloy.
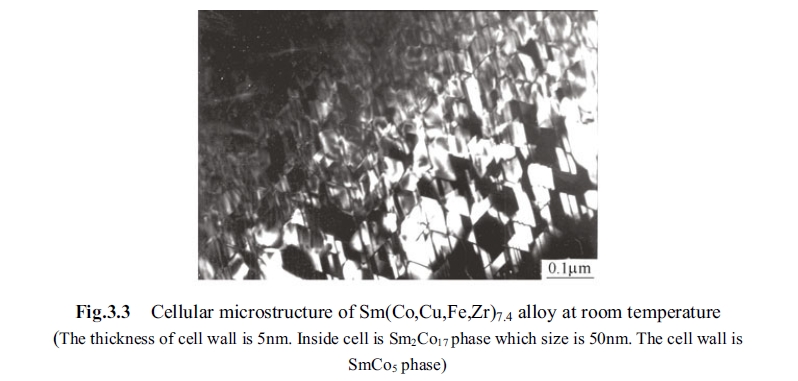
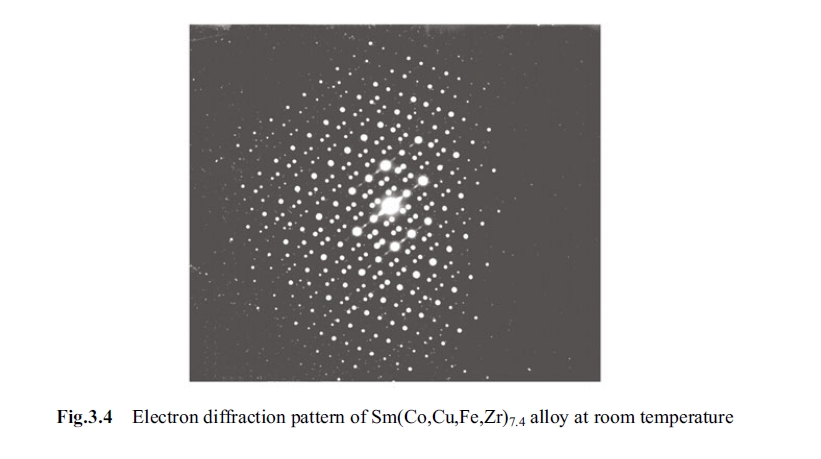
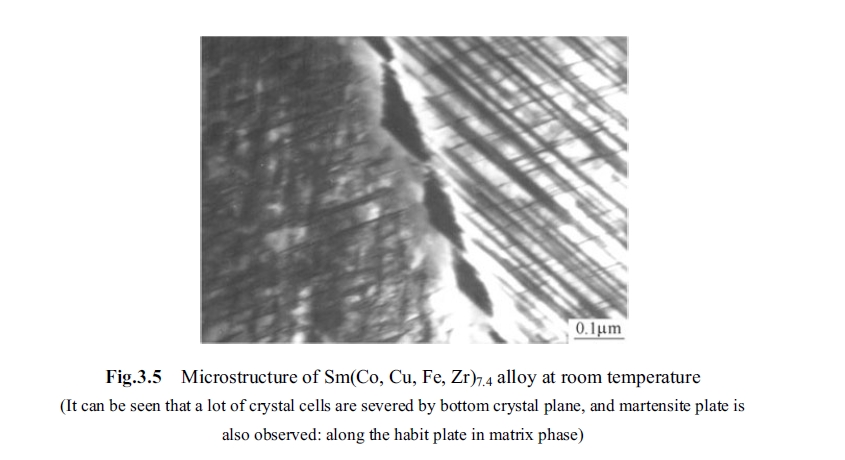
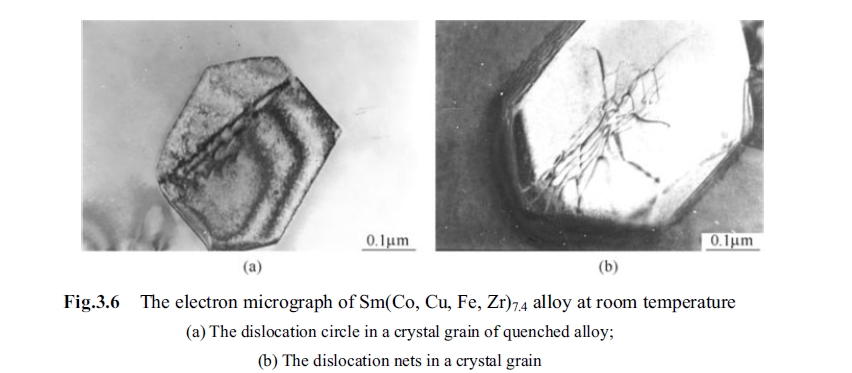
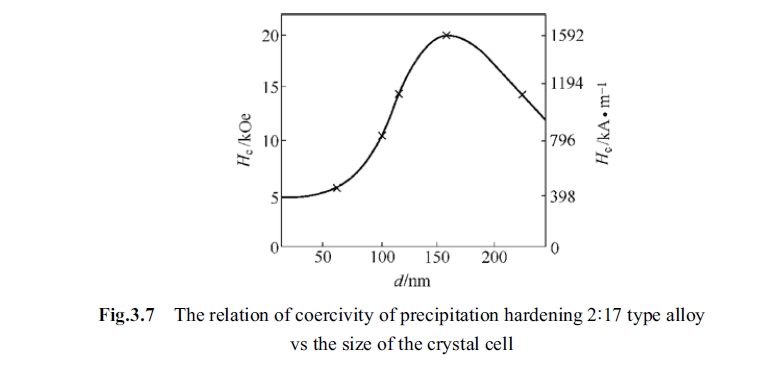
In-Situ and Dynamic Observation of Precipitation, Growth, and High-Temperature Phase Transformation of the Cellular Structure
The dynamic observation result of this experiment showed that cellular texture was extraordinary stable from 700°C to 840°C. Integrated cellular structure was observed again after heat preservation for 80min at 900°C, which illustrates the reversibility of the phase transformation.
The positioning in situ and dynamic observation process on the phase transformation
There were some discussions about the relationship of cellular texture and coercivity being heard before our experiment study, such as the cellular texture began to be formed at 700°C (Fidler, Skalicky, 1982; Sun, et al, 1983) and was destroyed at constant temperature aging at 800°C (Cai, Rong, 2003). Some changes might happen to inner-cell and cell wall at 830°C (Xu, Kong; Kronmiller, 1982), cellular texture was formed after aging at 830°C for 30min and cell wall varied at 830°C. Thus some cell would swallow the small one. And that the influence of long term aging on coercivity was attributed to the appearance of zirconium enriched long lamellar phase (Table 3.1). These conclusions, surmise and deducing were primarily deduced from observations at room temperature and in - advance designed big specimen and aging condition as per the deduction. And thus these were difficult to avoid unilateralism. To overcome this point we adopted filmy specimen being heated from room temperature to 950°C serially in transmission electronic microscope so that to observe directly the variation of micro - texture at every temperature section (different aging condition). We observed appearance, upgrowth and formation of cellular texture; and appearance, change, etc. of zirconium enriched long lamellar phase. This section concludes above problem based on experiments as follows:

1. It is found that cellular texture of permanent magnet alloy appeared at 460°C and its shape was spherical (see Fig. 3.8). The coercivity of the alloy was very sensitive to diameter and size of cellular texture. Their relationship is shown in Fig. 3.7.
2. Cellular texture started to form at 460°C (Fig. 3.9), and grew and developed at 500 - 600°C; the cellular texture size was different at 500 - 600°C, some were
grew up but some did not form integral cellular texture and some were only in embryo. Integrated cellular texture appeared at 700°C, they came to perfect at 790°C (Fig. 3.10 to Fig. 3.13).

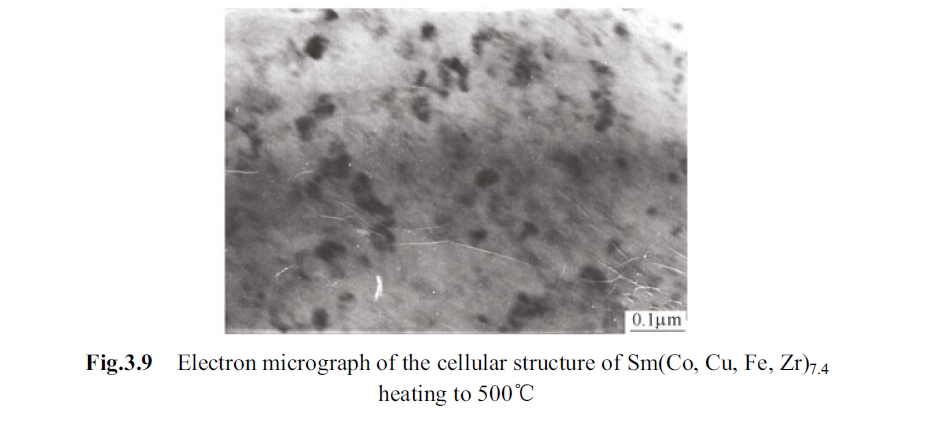
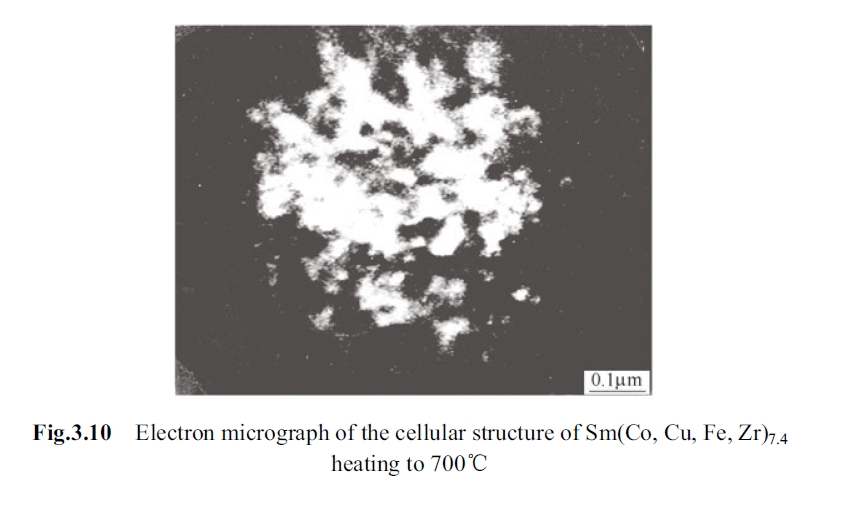
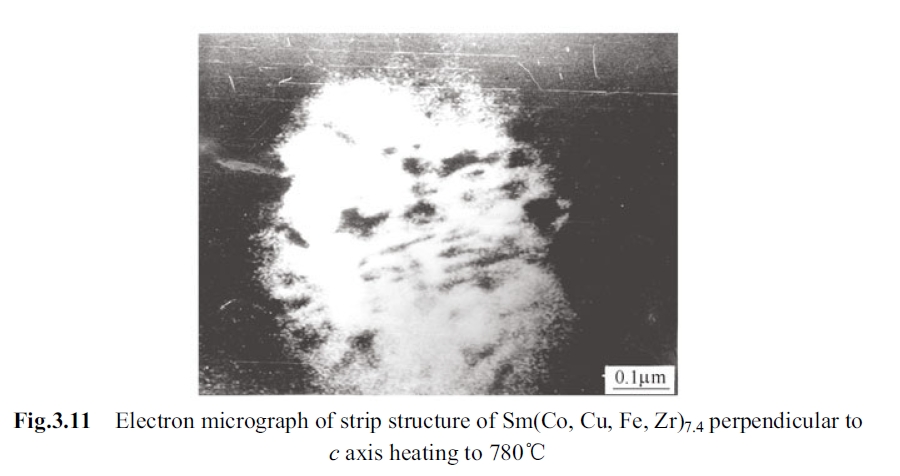
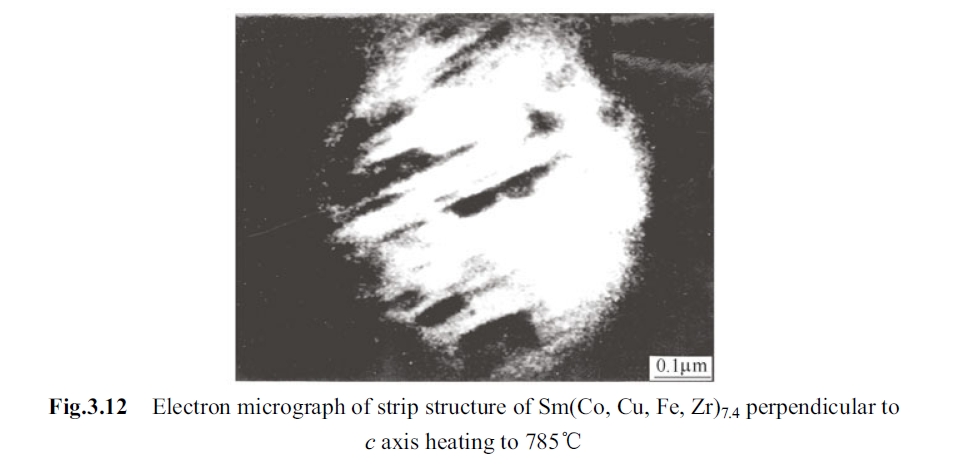
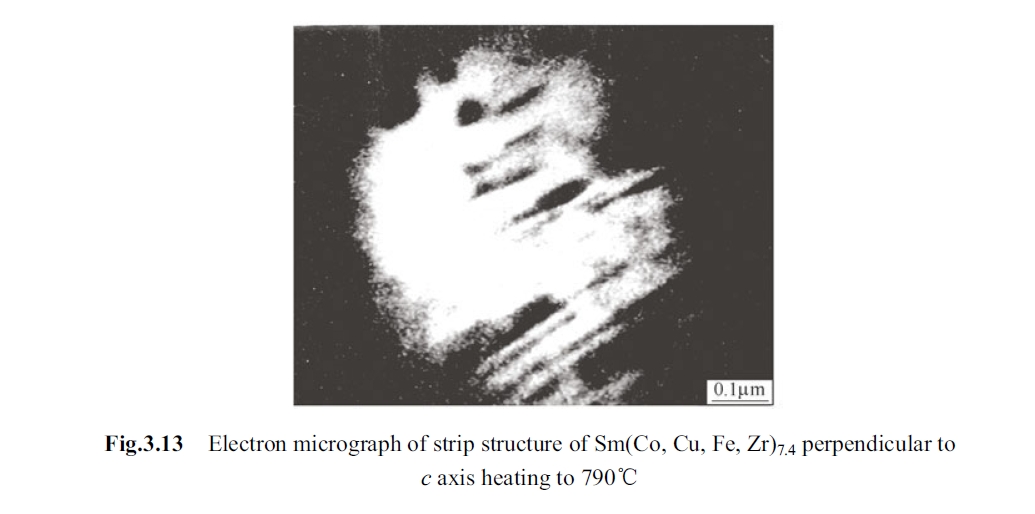
3. Lamellar phase, which is perpendicular to c axis, appeared at 780°C, but only partly in visual field. At 850°C, it appeared in most of visual field. And at 790°C, the lamellar phase being perpendicular to c axis appeared at the foundation of cellular structure (some called this phase as Z phase and some called as zirconium enriched long lamellar phase).
4. Cellular texture and lamellar structure coexist at 800°C (seeing Fig. 3.13 and Fig. 3.14).
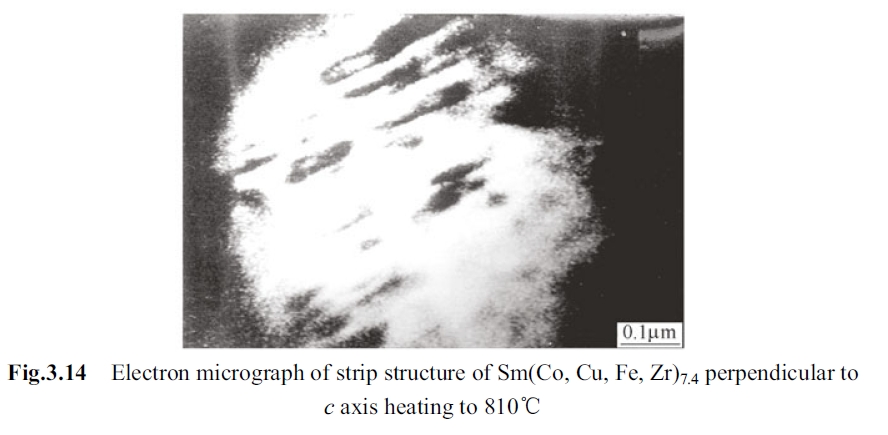
5. Lamellar phase (Z phase) aforementioned upgrowth at 820°C.
Lamellar phase increases gradually in company with continually rising of aging temperature. Fig. 3.14 is the lamellar phase growing on original situs at 810°C. Fig. 3.15 is the lamellar phase growing on original situs at 820°C. Fig. 3.16 is the lamellar phase growing on original situs at 830°C. The lamellar phase at 840°C and holding for 0.5h. It can be seen from Fig. 3.17 that the lamellar phase runs through all the vision.


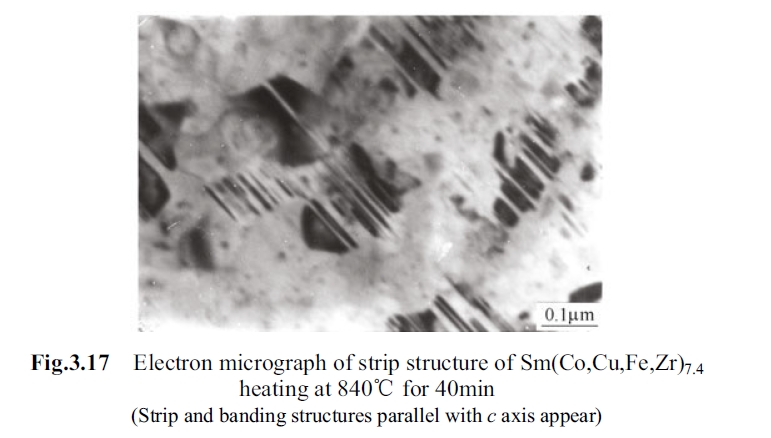
Some striation material and strip material being parallel to c axis appeared at 840°C and holding for 40min, the composition of these materials are still unknown.
Analysis and discuss on magnetic performance and heat treating system
\(Sm(Co, Cu, Fe, Zr)_{7.4}\) permanent magnetic alloy is a kind of precipitation hardening permanent magnetic alloy and the production of coercivity comes from the pinning relative to domain wall by \(Sm(Co, Cu)_5\) enriched phase precipitated in aging process (Pan, Ma, Li, 1993). Pinning intensity of \(Sm(Co, Cu)_5\) on domain wall depends on its shape, amount and composition difference from the base phase. Although \(Sm(Co, Cu)_5\) phase precipitated generally from the base phase at 460°C but this time these cellular wall phase did not fully connect together and that the copper in the base phase still could not defused fully to cellular wall because of the comparative low temperature, i.e., in this time the different between domain wall and inner cell is not big enough. Thus no matter the embryo shape of the cellular texture already formed at this temperature but did not acted obvious hardening function on the coercivity, which is consistent with the result shown in Fig. 3.18 (Pan, Zhao, 1988).
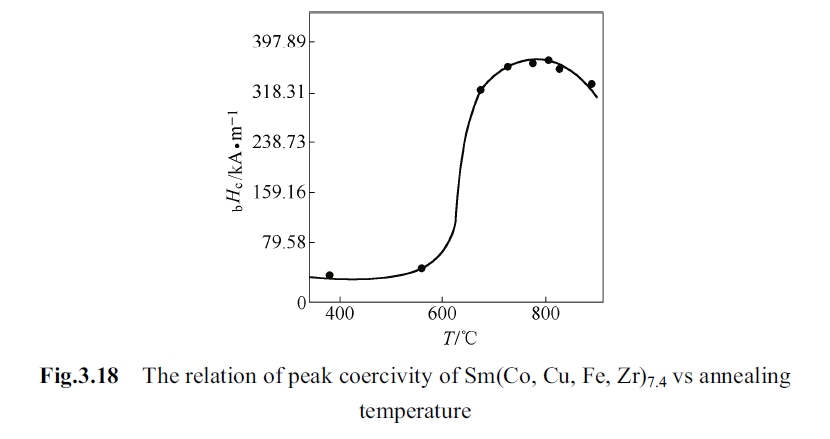
When the temperature was over 700°C, the cellular texture grew up adequately and the cellular connected together thus the copper content in inner cell and cell wall so the difference between domain wall energy of inner cell \(\gamma_{domain}\) and domain wall energy of cellular wall was big enough. Therefore \(_{m}H_c\) increased rapidly as per \(_{m}H_c = (\gamma_{domain}-\gamma_{wall})/(2M_s\delta)\) (Fig. 3.7) (Pan, Ma, Li, 1993).
Alloys with different types coercivity could be obtained by changing heat treatment condition of \(Sm(Co, Cu, Fe, Zr)_{7.4}\) alloy, and its demagnetization curve is shown in curve Ⅰ and Ⅱ of Fig. 3.19 (Xiao, Zhang, Zhou, et al, 1982). Their respective heat treatment system is shown in Fig. 3.20.
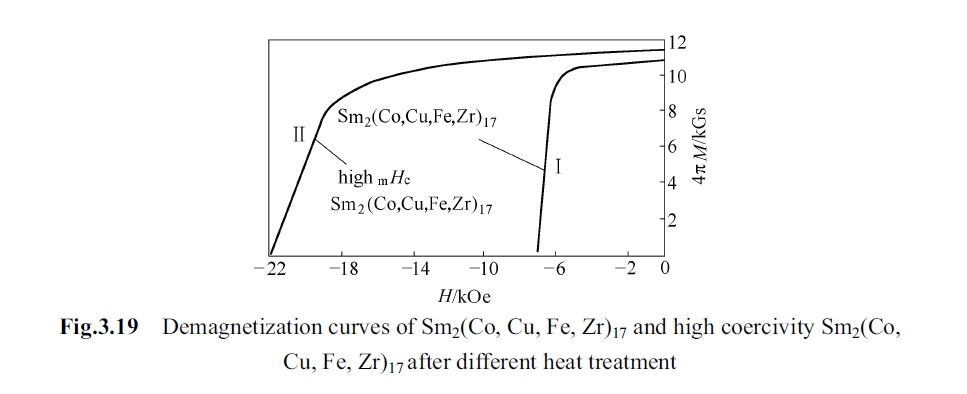
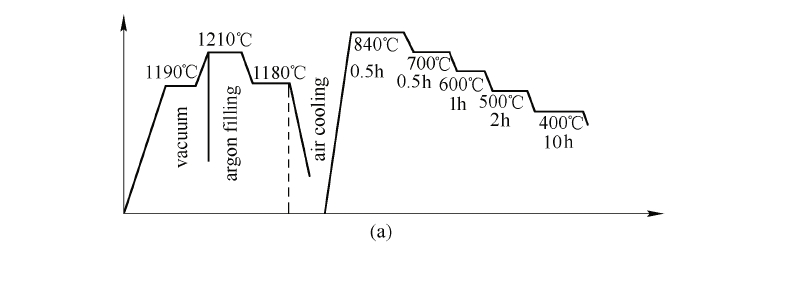

The formation, growth and growth velocity of cellular texture
Precipitation appeared in specimen at 300 - 400°C in dynamic observation and this decomposed precipitate was coherent with the matrix phase. These tiny spheric precipitates with a size of several nanometers were observed in transmission electronic microscope and these decomposed material made the system with very high interface energy. In this time, overall system was in unstable state under heat activation. To reduce the total interface energy small particles in the decomposed grain dissolved, the large ones grown up and continually dissolved other components. Fig. 3.21 shows the longitudinal section figure of Sm - Co - 13Cu - 10Fe (Cu > Fe) in which samarium accounted for 10% - 16% (at.). There are four phases in the figure: L is liquid phase, Co phase is cobalt based solid solution, 2:17 phase (three structures of \(Th_2Ni_{17}\), \(Th_2Zn_{17}\), and \(TbCu_7\)), and 1:5 phase. At 1210°C the solubility of 2:17 phase relative to samarium reaches up to 13% from 10.5% (both in atomic fraction). In this composition its melting point is lower along with increase of samarium content. The alloy with samarium of 11.9% - 12.5% (atomic fraction) is of \(TbCu\) type structure at 1210°C, and the homogenizing treatment in \(TbCu\) phase region can obtain a comparative higher coercivity. Structure of 2:17 phase is related to content of iron and copper contents that the alloy with 2.0% zirconium and 11.5% samarium has \(TbCu\) type structure at high temperature. The \(_{m}H_c = 2000\) kA/m may be reached after solid solution treatment and aging (Zhou, 1990). Generally speaking, there are only two constituents and solubility of one constituent in the other constituent is limited and the solubility will become smaller while the temperature becomes lower, as is shown in Fig. 3.22. One type of constituent dissolving into an \(\alpha\) solid solution and then quenching to suppress the precipitation of this constituent to reach saturated solid solution is called as solid solution treatment. The reverse process of solid solution treatment is decomposition. The hardness and intensity of the alloy would be improved in decomposition process, namely aging hardening. At the anaphase of decomposition equilibrium phase appears by decomposition. During the dynamic observation of 300 - 600°C, bulky grain grown up and coarsened after dissolving with small particles, so concentration gradient exists consequentially between bulky grain and small particles.
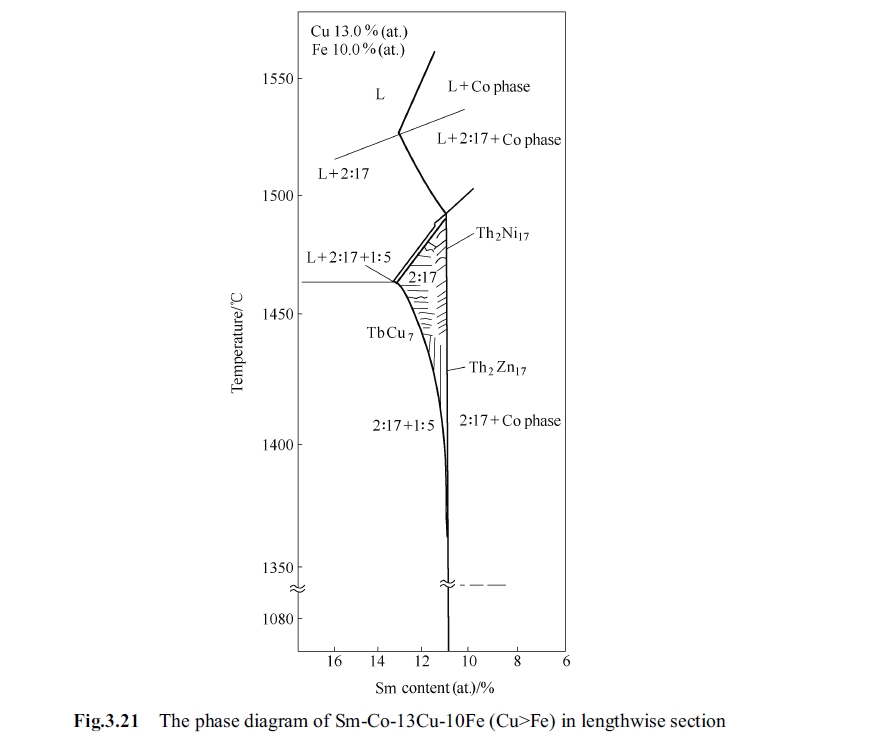
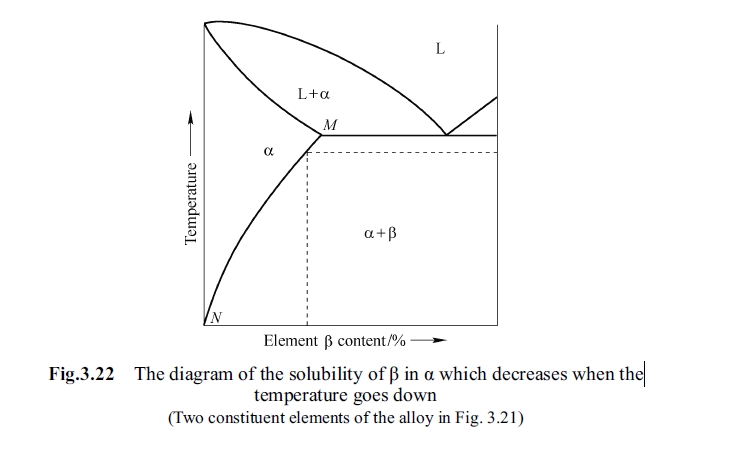
the dynamic observation it takes 6min from beginning to 460°C, and takes 12min from 460°C to 600°C. It was found in dynamic observed at 600°C some cellular textures began to grow up but their size was very different and most of them were in embryo. There was no integrated cellular texture. Temperature was raised in the electronic microscope and it took 6min from 600°C to 700°C. At this temperature the integrated cellular texture was observed (Fig. 3.10). Fig. 3.23 is the sketch map of formation process of cellular texture and Table 3.2 shows the growth time.
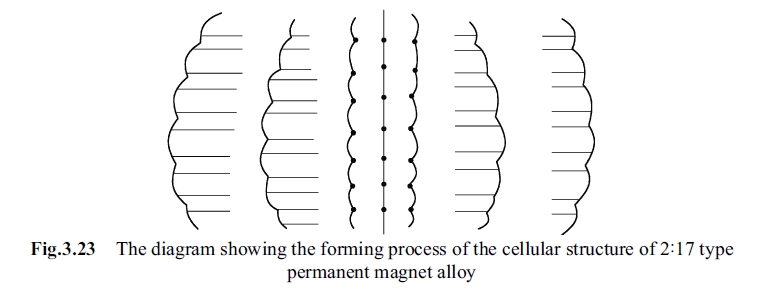
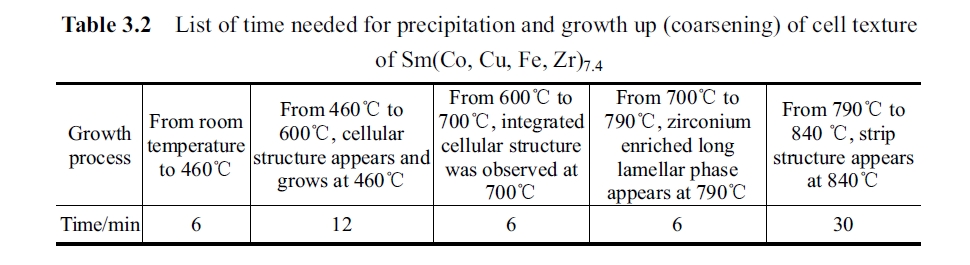
According to diffusion control grown up theory, can we figure out the growth velocity of cellular texture from precipitation to integral one? It was observed that the cellular texture was orbicular, i.e., a sphere shape. Supposing radius is \(r_1\), solute quantity absorbed in unit time in growth process of cellular texture is \(4\pi r_1^2 (C_b - C_r)v\), where \(C_b\) and \(C_r\) are the interfacial volume concentration of precipitated phase, \(v\) is growth rate. Diffusion flux of particle is \(4\pi r^2 D(\mathrm{d}C/\mathrm{d}r)\). The following formulae are come into existence.
\(\frac{D\mathrm{d}C}{r_1^2 (C_b - C_r)v}=\frac{\mathrm{d}r}{r^2}\)
Supposing the \(C_{\overline{r}}\) is the concentration of the base phase being equivalent to average granule radius \(\overline{r}\) of granules system corresponding to solubility (Yu, 2003). By integrating \(r\) from \(r_1\) to \(\infty\), \(C\) from \(C = C_r\) to \(C = C_{\overline{r}}\), it can be derived that:
So growth velocity \(v\) is:
Analyzing on driving force and resistance of cellular texture and phase transformation
During the phase transformation process of the alloy, no matter nucleation or not, phase transformation always encounters driving force and resistance. Thus for phase transformation energy proceeding spontaneously a necessary premise is that the free enthalpy of new phase less free enthalpy of old phase is minus. If \(Q\) represents for the resistance of phase transformation, then \(Q=\Delta G_1 + \Delta G_2\), \(\Delta G_1\) represents for interfacial energy and \(\Delta G_2\) represents for distortion energy. Interfacial energy is divided into chemical interfacial energy and structural interface energy. There are four kinds of property of interface, and that is ideal coherence, complete coherence, partial coherence and non - coherence. Interfacial energy of complete coherence is very small, and mismatch degree of interface atom is zero. The mismatch degree of non - coherence is the maximal. The degree mismatch of complete coherence is: \(\delta=\Delta a/a\lt0.05\); mismatch degree of partial coherence is: \(\delta = \Delta a/a = 0.05 - 0.25\) (Liu, Ren, Song, 2003). Table 3.3 shows the lattice constant and lattice mismatch caused by precipitation of 1:5 phase in the 2:17 base phase.
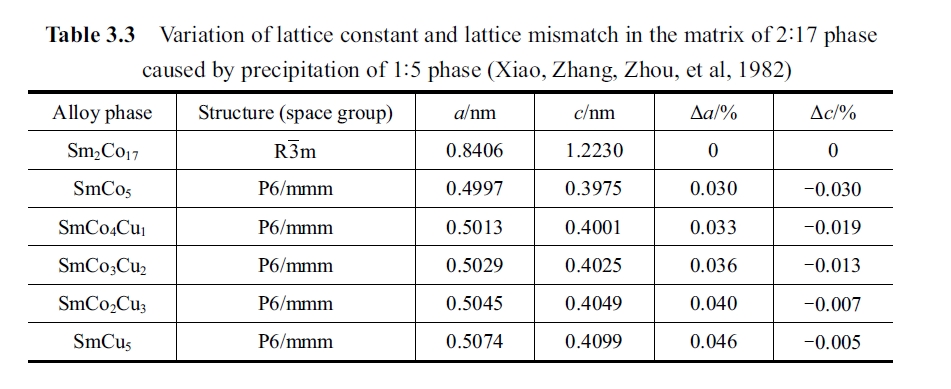
The distortion energy is divided into coherence distortion energy and non - coherence distortion energy. Coherence distortion energy: shear elasticity coherence distortion energy is related to the rotation angle \(\varphi\) of atomic plane, matrix phase shear modulus \(G\) and shape of new phase in phase transformation. Supposing distortion occurs in matrix phase, volume distortion energy is approximate as \((3/2)E\delta^2\), where \(E\) is elastic modulus and \(\delta\) is mismatch degree that \(\delta = \Delta a/a\). Anyway shear elasticity distortion energy and shape factor are closely related to each other (Liu, Ren, Song, 2003). Fidler J. thought that the coercivity of precipitation hardened the 2:17 type alloy was determined not only by domain wall energy gradient \(\Delta\gamma\), but also by magnetoelastic coupling energy between domain wall magnetostrictive stress and precipitated phase strain, that is to say, the contribution lattice mismatch degree of 1:5 phase and 2:17 phase to the coercivity is not neglected. That can be formulated: \(_{m}H_c\approx|\sigma_{11}\Delta a|/(3M_s)\) (Zhou, 1990; Fidler, 1982). It was found in the in situ and dynamic observation of experimental specimen that the \(Sm_2(Co, Cu, Fe, M)_{17}\) main phase, which took 50min from precipitated cellular embryo coarsening and upgrowth to integrated organization structure, was surrounded by \(Sm(Co, Cu, M)_5\) border phase of 10nm in thickness only took 6 min. Table 3.2 and Fig. 3.10 testified the precipitation of above mentioned \(Sm(Co, Cu, M)_5\) phase, and the transformation did not need very big nucleation power, incubation period (that the critical crystal nucleus must jump over the energy barrier is the nucleation power) so that it is easy to complete from embryo to integral cell structure of 1:5 phase. When diffusion driving free energy \(\Delta G\lt0\), or \(G''=(d^2G/dC^2)\lt0\), the very small fluctuation will be formed and this small fluctuation with certain wavelength provides a condition for new phase up-hill diffusion that \((d^2G/dC^2)\lt0\) (Xu, 2000). It is also found from the dynamic observation in this experiment that cellular texture was extraordinary stable from 700°C to 840°C, seeing Fig. 3.28. From the zirconium enriched lamella phase running through at 790°C to completely drilling through the 1:5 phase it was still stable, this is testified experimentally that the precipitation of 1:5 phase needed to along pyramidal plane of which lattice misfit was zero and a long rhombic cell was formed (Fig. 3.13 and Fig. 3.28). It is also found from dynamic observation of the experimental specimen that the strip, nubby and anomalous geometrical shape appeared at 840°C and holding for 40 - 80min (Fig. 3.24 to Fig. 3.28). As shown in Fig. 3.29, integrated cellular microstructure reappears when cooling back to room temperature from 80min heat preservation at 900°C, which illustrates the reversibility of the transformation heat.






Kinetics analysis on phase transformation
In the following to focus on discussing the phase transformation kinetics analysis on the phenomenon in dynamic observation of \(Sm(Co, Cu, Fe, Zr)_{7.4}\) specimen. In viewpoint of phase transformation kinetics: in homogenous single - phase or several mixed phases appeared variation of phase with different composition or position of different ions, atoms and electron, and exposure (different structure), character, different configuration, being so called as phase transformation. Thus that the phenomenon of specimen appeared after holding for 1h at 840°C belongs to phase transformation category. During phase transformation, the matrix phase became unstable and decomposed into stable two phases and their free energy was lower than that of the matrix phase. When different concentration fluctuation appeared in the matrix phase the free energy and nucleation power (nucleation driving force) all could be derived from the intersection of tangent and free - energy curve (Xu, 2000). When concentration fluctuation appeared and the concentration exceeding a given level, i.e., exceeding the critical value of free energy change will actually become the energy barrier which one crystalline nucleus has to exceed that an embryo is smaller than the critical size it will be dissolved back to the matrix phase spontaneously and the size of one embryo is bigger than the critical size it will grow to be a crystalline nucleus and continually grow up to new phase. Nucleation field could be deduced by specimen in this experiment and its value can be estimated as follow:
Theoretical minimal value of nucleation field \(H_n\) can be calculated by following formula:
Nucleation field can be derived from formula above:
where \(M_s\) is the saturation magnetization intensity; \(\gamma\) is the energy density of domain wall; \(a\) is the length of hexagonal prism one side; \(h\) is the height of the hexagonal prism.
Supposing the reversal magnetization nuclear radius is \(R\) and when \(R = 10\)nm, it can be calculated that \(H_n\) is 2,388 kA/m and similarly when \(R = 100\)nm, \(H_n\) is 238 kA/m.
Defects appeared in cellular texture after holding about one hour at 840°C, that is to say, \(a\), \(h\) and \(R\) increase in the above calculation and that nucleation field \(H_n\) decreases, so that coercivity will degrade remarkably. It was observed from fore photographs Fig. 3.24 to Fig. 3.27 that defects appeared in new precipitated and thus holding for long time at 840 - 860°C caused degradation of coercivity. That these very low anisotropy areas existed in a considerable volume in new precipitated phase caused degradation of coercivity, as shown in the curve in Fig. 3.18.
Coercivity mechanism after destroying of cellular texture by long time aging at high temperature
When long time aging at above 840°C and the cellular texture began to be destroyed the \(Sm(Co, Cu, Fe, Zr)_4\) alloy and its coercivity was controlled by nucleation and local pinning. The so - called coercivity controlled by nucleation field is determined by the magnetic field which is necessary for building reversal magnetization nucleus, such as inhomogeneous grain boundary, irregular surface, oxidation and other form defects. It is preferential to become reversal magnetization nucleation center for these regions with low magnetocrystalline anisotropy, and thus to enhance coercivity it is necessary to avoid these defects. If pinning position is just in near nucleation site and to limit extending of the reversal magnetization nucleus the coercivity will be enhanced. It was found through dynamic observation in this experiment that there was big and integral cell structure and local high density dislocation network, which promote the appearance of decomposition copper granules so that to become the pinning position. These are sufficient condition and key factor for alloy specimen to have a higher coercivity. For this kind of alloy to enhance coercivity should select aging temperature below 840°C, for example, 800 - 830°C would be a good choice.
For the alloy of \(Sm(Co, Cu, Fe, Zr)_{7.4}\) its coercivity is determined by pinning field. The pinning center is cellular texture of 2:17 phase 80% surrounded by 1:5 phase 20% with a thickness of 10nm. The 1:5 phase acts as pinning function on domain wall. The coercivity of cellular texture is:
where \(M_s\) is the saturation magnetization intensity; \(\delta\) is the thickness of magnetic domain wall; \(d\) is cell diameter; \(\Delta r\) is energy difference of domain wall:
Energy difference of domain wall is mainly decided by magnetic anisotropy constant \(K_1\) of 1:5 phase and 2:17 phase and exchange integral \(A\). The \(A\) and \(K_1\) are mainly determined by composition and defects.
It was seen in the in situ and dynamic observation by electronic microscope that cellular texture has formed at 700°C, zirconium enriched long lamella phase appeared at 790°C. In order to get this kind of alloy, the first grade aging should select 790 - 830°C to set temperature range and to find out the maximum peak of coercivity by experiment because the alloy of 1:5 phase is stable at 790 - 830°C.
Diffusion type continuous phase transformation
Above phase transformation of \(Sm(Co, Cu, Fe, Zr)_{7.4}\) permanent magnetic alloy belongs to diffusion type continuous phase transformation. Under continuous and ordered and fluctuation congregating and through uphill diffusion and congregation a single phase is disaggregated into \(Sm_2(Co, Cu, Fe, M)_{17}\) phase with a metastable size about 50nm and \(Sm(Co, Cu, Fe, Zr)_5\) phase about 10nm. The former is surrounded by the latter and these two phases are coherent. Any small fluctuation would make concentration amplitude heightened continually and to form new phase. The fluctuant concentration continuously changes with time, at beginning stage the interface between above mentioned 2:17 phase and 1:5 phases is not obvious; after disaggregating the size distribution of the 1:5 phase and the 2:17 phase becomes comparatively regular with highly continuity (Xu, 2000; Xiao, 2004).
It was observed from the specimen of this experiment that the nucleus of embryo was diffusion nucleation: the course is to form new phase core first, namely giving birth to nucleus. The fluctuation of nuclei embryos or new phase points rely on diffuse transition of individual atom by thermal activation and gradient of free energy as driving force of phase transformation. Solid state phase transformation belongs to inhomogeneous nucleation.
Metastable transitional phase
After the metastable transitional phase being aging for 20h at 830°C its cellular texture become non-integrated any more that part of them have been destroyed and a few of them become trip structure, this trip structure might belong to a transitional phase. When temperature was raised to 1050°C or lower to 820 - 800°C the transitional phase transforms into stable phase of 1:5 phase and 2:17 phase with cellular texture.
The experiment indicated: in order to get rapidly increase of \(_{m}H_c\) aging time should not be less than 2h at 840°C.
Many researchers considered that the influence of long time aging on coercivity was attributed to appearance of zirconium enriched long lamellar phase (sometimes called as Z phase) being perpendicular to \(c\) axis. The experiment in this section indicates that this long lamellar zirconium enriched phase began to form at temperature heated to 780°C. And when holding for 0.5h at 840°C this long lamellar phase has run through the whole visual field, seeing Fig. 3.17 and Fig. 3.18. This fact does not fit the result that coercivity enhanced greatly with holding at equal temperature of 850°C for 2h. Therefore, author believes that appearance of Z phase does not have direct contribution to high coercivity and is most possible to have indirect function, such as accelerating component diffusion as a passage or resulting in formation other new phase (Zhou, 1990; Pan, Ma, Li, 1993; Pan, Zhao, 1988). The function of zirconium sees the section 3.2 of this book.
Conclusions: Key Findings on Phase Transformation and Magnetic Properties of Sm(Co, Cu, Fe, Zr)₇.₄
1. The coercivity of \(Sm(Co, Cu, Fe, Zr)_{7.4}\) permanent magnetic alloy increases with quantity increases and upgrowth of cellular texture, and decreases with destruction and subtraction of cellular texture. Coercivity of the alloy is very sensitive to the pattern, size, upgrowth degree and quantity of cellular texture.
2. From room temperature to 800°C the process of temperature rising is a heat activation course. The heat activation is motivity for appearance, upgrowth and formation of cell texture. It controls atomic diffusion in components of the alloy. Owing to this heat activation function copper in alloy diffuse to cell wall gradually. When temperature is raised to above 700°C, the cellular texture would grow up adequately and cell wall would be interconnected, copper content in cell wall and interior of cell becomes big enough thereby it would result in that the domain wall energy difference between inter - cell and cell wall domain becomes sufficient big. Because coercivity is proportional to the difference of them thus coercivity increases the \(Sm(Co, Cu, Fe, Zr)_{7.4}\) permanent magnetic alloy could obtain various types of alloys with different coercivity through different heat treatment condition.
3. Cellular texture of \(Sm(Co, Cu, Fe, Zr)_{7.4}\) permanent magnetic alloy appeared at 460°C and its shape was spherical. It began to form at 500°C, grown and developed at 500 - 700°C, integrated structure formed at 700°C, and grown up perfectly at 790°C. The cellular texture would change when holding at 840°C for 40min.
4. It was found in the in situ and dynamic observation of \(Sm(Co, Cu, Fe, Zr)_{7.4}\) permanent magnetic alloy by transmission electronic microscope that the zirconium enriched lamellar phase (or called Z phase) being perpendicular to \(c\) axis appeared at 780°C and ran through the whole visual field and cellular texture at 830°C, but this lamellar phase had no direct contribution to coercivity of the alloy.
5. The precipitation and growth of the cellular texture of \(Sm(Co, Cu, Fe, Zr)_{7.4}\) permanent magnetic alloy is a complete process for cellular texture and phase transformation belonging to diffusion continuous phase transformation.
6. From precipitation of the cellular structure of the \(Sm(Co, Cu, Fe, Zr)_{7.4}\) permanent magnetic alloy to grow up perfectly at 840°C the coercivity of the alloy was determined by pinning field. After the cellular texture was destroyed coercivity of the alloy is determined by nucleation field.
7. Coercivity of \(Sm(Co, Cu, Fe, Zr)_{7.4}\) permanent magnets increases with the increase in the number, development, growth of cellular structure, decreases with the destruction and reduction of the cellular structure. The coercivity of alloy is sensitive to the morphology, structure, size, development process and the number of the cellular structure. Alloys with different coercivity can be obtained through different heat treatment conditions. From room temperature to 800°C, the process is a thermally activated process. This process is the driving force for the emergence and development of cellular structure, which dominates the diffusion of the atoms in the alloy composition.
8. For \((Sm_{1 - x}Gd_x)(Co, Fe, Cu, Zr)_z\) magnets, with the increase of \(z\) magnet remanence temperature coefficient firstly increased then reduced under the same temperature. When \(z = 7.87\), remanence temperature coefficient reaches a minimum, the most stable magnet has the largest coercivity (Pan, 2011).