Rubber Magnet
- Home
- Rubber Magnet
Rubber Mounting Magnets
Rubber magnets are lightweight and highly flexible, making them ideal for various applications. These magnets can be cut, twisted, or shaped without losing magnetic properties, allowing for customization to meet specific needs. Perfect for signage, crafts, and educational tools, they are widely used in schools, offices, and homes. Their resistance to moisture and chemicals ensures durability, even in challenging environments. Whether you need magnetic labels, seals, or creative project materials, rubber magnets provide a reliable and versatile solution. With their ability to combine functionality and adaptability, they cater to both personal and industrial purposes, offering unmatched convenience and performance.
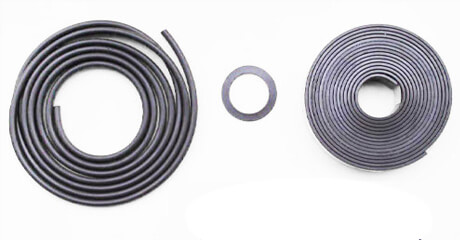
Key Features and Benefits of our Rubber Mounting Magnet
- Protective Rubber Coating: Guards against surface scratches and damage, ideal for use on delicate or finished surfaces
- High Magnetic Strength: Neodymium magnets offer strong holding power, securely attaching items where needed
- Corrosion Resistance: The rubber coating provides an additional layer of protection against moisture and chemical exposure.
- Durability: The rubber encasement helps absorb shocks and impacts, extending the life of the magnet.
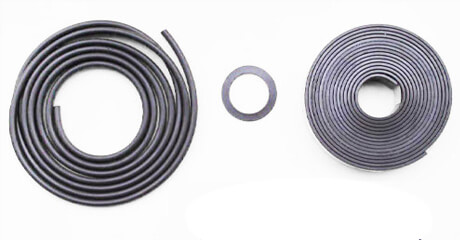
Key Features and Benefits of our Rubber Mounting Magnet
- Protective Rubber Coating: Guards against surface scratches and damage, ideal for use on delicate or finished surfaces
- High Magnetic Strength: Neodymium magnets offer strong holding power, securely attaching items where needed
- Corrosion Resistance: The rubber coating provides an additional layer of protection against moisture and chemical exposure.
- Durability: The rubber encasement helps absorb shocks and impacts, extending the life of the magnet.
Our Related Product
The Composition of Rubber Magnets
Magnetic Powder
At the base of rubber magnets, lies magnetic powder which is primarily drawn from ferrite compound (iron oxide). The ferrite is often supplemented by other elements like strontium and barium.Alternatively, rare earth magnetic materials can be crushed and their powder utilized as the base of rubber magnets. The magnetic powder is the force behind the rubber magnets’ magnetic capabilities.
Polymer Binder
The powdered magnetic particles must be enjoined and this is achieved with the aid of polymer binders. The most commonly utilized polymer binders in rubber magnets include polyvinyl chloride (PVC) and flexible plastics. The binder is responsible for the flexibility exhibited by rubber-coated magnets. Other additives may be injected into rubber magnets to elevate specific features like coloration and physical strength.
Magnetic Properties of Rubber Magnets
Rubber magnets can be differentiated from conventional inelastic magnets easily.This is because they possess distinct characteristics like elasticity and corrosion resistance. Underneath are the primary properties that set apart rubber magnets from typical magnets.
Magnetic Strength
Rubber magnets are primarily designed for applications that prioritize flexibility rather than strong magnetic forces. As such, they exhibit relatively inferior magnetic strengths compared to rigid magnets like neodymium magnets. This means that their maximum energy product (BHmax) is comparatively lower.
Flexibility
Although they do not exhibit strong magnetic forces like conventional rigid magnets, rubber magnets are unmatched when it comes to flexibility. They can be bent, twisted, or even molded into varying shapes depending on the respective scenario. The elasticity property is enabled by the flexible polymer binders added to the magnetic powder.
Coercivity
Rubber magnets tend to lose their magnetic powers more easily compared to other magnet types. This, however, does not mean that they are easily demagnetized because they can retain their magnetism even under the presence of stronger magnetic fields. Comparing their resistance to demagnetization to rare earth magnets is however a mismatch.
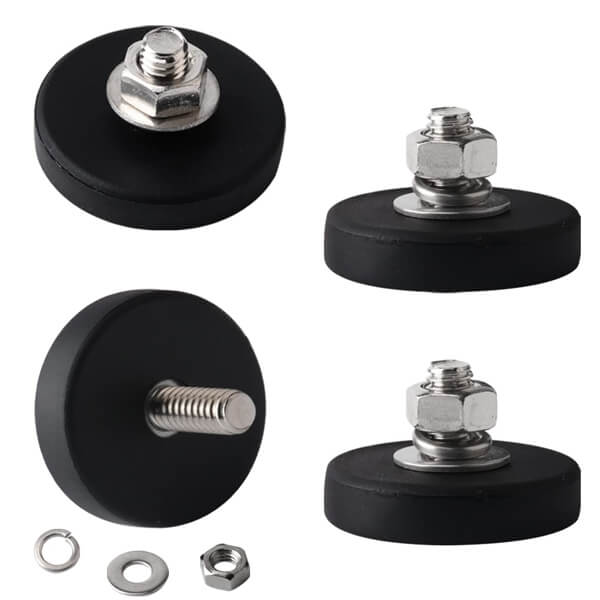
Classifications of Rubber Magnets
In anisotropic rubber magnets, the magnetic domains are uniformly aligned and this is because they are magnetized during the curing process.
This equips them with more powerful magnetic forces, unlike isotropic magnets. They are however weaker when it comes to flexibility. Anisotropic flexible magnets are therefore commonly utilized in applications prioritizing stronger magnetism rather than elasticity.
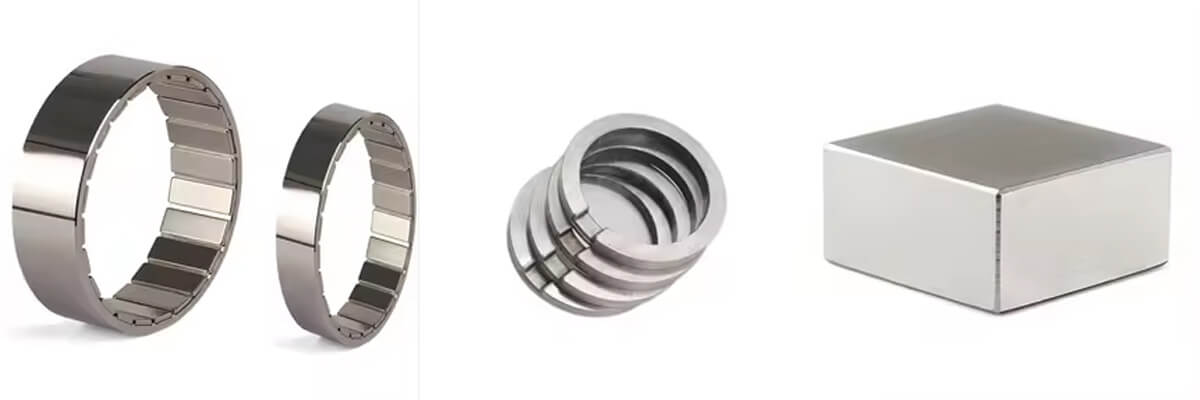
Rubber Magnet Manufacturing Process
- Ingredient Preparation: Rubber magnets commences with the collection and preparation of the main ingredients. Besides, these ingredients are magnetic material powder, polymer binders, and optional additives. The amounts are precisely calculated to ensure uniformity in the rubber magnet’s magnetism.
- Mixing: With all the ingredients in place, the magnetic powder is placed in a mixer and the polymer binder is added. The two compounds are then mixed thoroughly until a uniform distribution is achieved.
- Calendaring: The resulting mixture is then injected into a calendaring machine where rollers flatten and shape the mixture. This results in flat sheets or rubber magnetic material evenly sized.
- Magnetization: The evenly sized material collected from the calendaring machine is then introduced to power magnetic fields. This helps align the magnetic domains of the magnetic material resulting in active magnetic forces. This can be repeated severally to ensure optimal magnetization.
- Curing: The curing process involves subjecting the magnetic material to controlled heat. Varying heating methods can be employed to achieve curing but the most common involves using ovens.
- Shaping : Consequently, the magnetized material is cut into smaller pieces as per the design demands. Laser cutting is often used to cut rubber magnets into different shapes and designs.
- Surface Treatment: Although this step is optional, it is often utilized. Surface treatment can include adding protective coatings or printable materials for branding.
- Quality Control : Finally, the rubber magnets are subjected to multiple tests to guarantee quality. The magnetic strength is measured as well as the magnet’s elasticity.
Customizable Rubber Magnets for All Applications
- Durability: Rubber magnets are resistant to demagnetization, corrosion, and breakage. The rubber coating provides a protective barrier against environmental factors such as moisture and chemicals, ensuring longevity even in challenging environments.
- Temperature Stability: These magnets maintain their functionality across a broad temperature range, typically from -40°C to 80°C. This stability makes them suitable for applications exposed to varying thermal conditions.

rubber mounting magnets
rubber mounting magnets FAQs.
What are rubber mounting magnets?
Rubber mounting magnets are permanent magnets, usually made of neodymium or ferrite, coated in a protective layer of rubber. This coating enhances the magnet’s durability, provides corrosion resistance, and prevents scratching of surfaces with which the magnet comes into contact.
What advantages do rubber mounting magnets offer?
Surface Protection: The rubber coating prevents scratches and dings on the surfaces where the magnets are applied. Increased Durability: The rubber provides a cushion that absorbs impact, reducing the risk of the magnet chipping or cracking from falls or collisions. Corrosion Resistance: The coating protects the magnet from moisture and chemical exposure, prolonging its lifespan. Enhanced Grip: Rubber has a higher friction coefficient than metal or plastic, which helps the magnet stay in place without sliding.
What are the typical applications for rubber mounting magnets?
How strong are rubber mounting magnets?
Can rubber mounting magnets be used outdoors?
How are rubber mounting magnets installed?
Can the rubber coating be customized?
Are there any safety concerns with rubber mounting magnets?
Rubber Coated Mounting Magnet
Construction of Rubber Coated Magnets
Durable and Customizable Rubber Magnets for Every Need
Our rubber magnets combine durability and flexibility, making them the perfect choice for diverse applications. Manufactured using premium materials, they offer excellent magnetic performance while being resistant to wear, moisture, and harsh environmental conditions. These magnets are ideal for crafting, educational purposes, magnetic signage, and industrial solutions. Their ability to be cut and shaped with ease allows for maximum customization, ensuring they fit seamlessly into any project or setup. Whether you need lightweight materials for advertising or robust magnets for technical applications, these magnets deliver consistent performance. Designed to withstand the test of time, they are a reliable choice for businesses, educators, and DIY enthusiasts. Experience the convenience and adaptability of our rubber magnets, tailored to meet your exact needs with precision and quality.
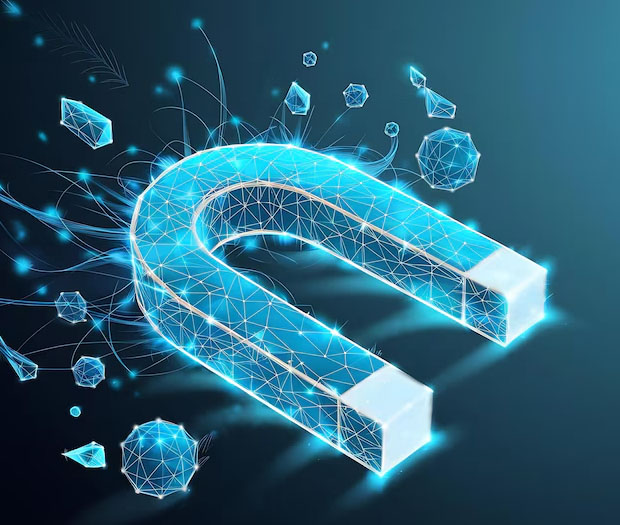
what client say of our Rubber Magnet
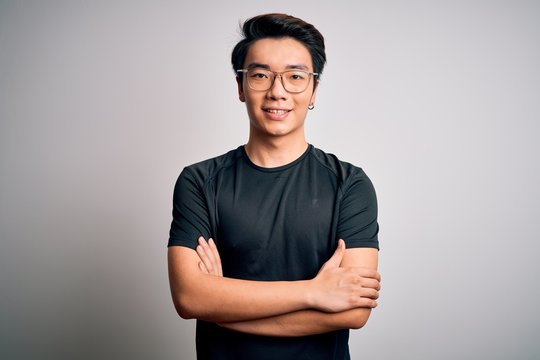
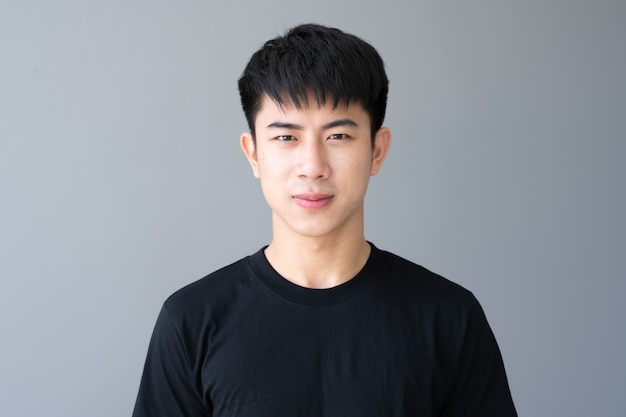
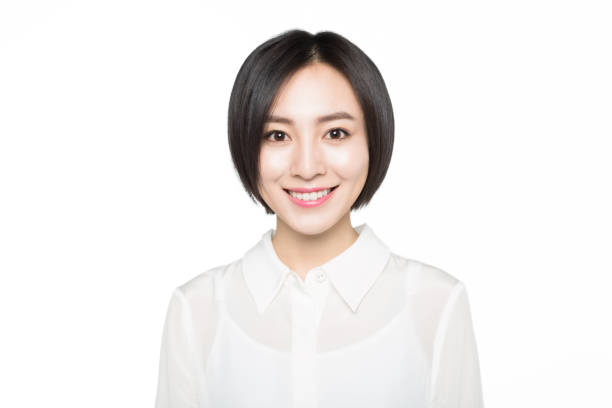