Ferrite Magnets
- Home
- Ferrite Magnets
What is a Ferrite Magnet?
Ferrite magnets cost much less than other permanent magnets and display high resistance to demagnetization. They however display lower magnetic strength compared to these magnets but still with substantial magnetic force.
Ceramic Ferrite Magnets
Ferrite or ceramic magnets are a type of permanent magnet made from a composite of iron oxide (Fe2O3) and one or more additional metallic elements, typically barium (Ba) or strontium (Sr) carbonates. These magnets belong to the category of hard ferrites and are characterized by their good resistance to demagnetization, excellent corrosion resistance, and affordability.
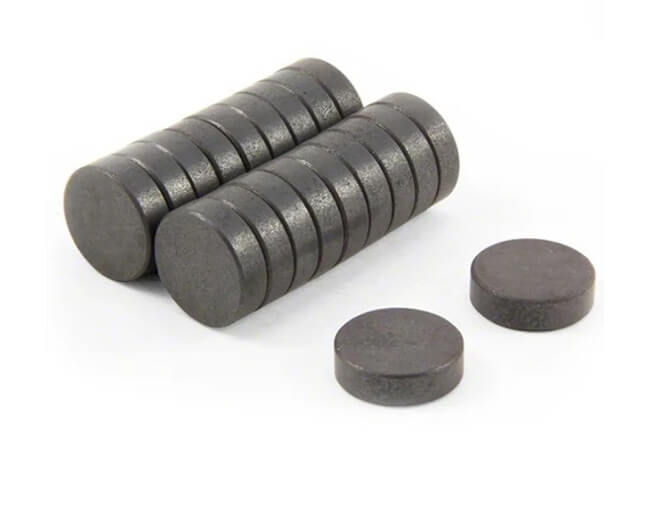
Our Related Product
Manufacturing Process of Ferrite Magnets
Raw Material Preparation
The process of raw material preparation involves carefully weighing the selected raw materials depending on the final magnet composition. A homogeneous blend is then developed by thoroughly mixing these materials.
Mixing
Dry mixing is utilized where the raw materials are in powder form blending them directly. Here, the powders are added to a mixing vessel, where they’re mechanically agitated to achieve a uniform blend.
In wet mixing, a slurry is created by adding water or a solvent to the powdered raw materials. The resulting sludge is then mixed to achieve uniform component distribution. Wet mixing can improve homogeneity and the raw materials’ chemical interaction.
Mixing equipment such as high-energy mixing mills, planetary mixers, and ribbon blenders are used to achieve thorough mixing. These mills use mechanical force to combine the materials into a single strain. When mixing, consider important parameters like mixing time and agitation speed.
Calcination
The temperature during calcination shouldn’t be too high to prematurely commence sintering. The process is ideally carried out in the presence of air or controlled atmospheres with reducing/inert gases to prevent oxidation. The process can take anywhere from several hours to a day.
Wet Milling
Ball mills containing grinding media like small beads/balls of steel, ceramic, or glass materials find use in the wet milling process. The process is conducted in a controlled environment to prevent contamination and ensure consistent processing conditions.
Forming
Dry Pressing: Involves the use of a mechanical press to compact the material in a mold under pressure resulting in a solid structure. It can easily execute simple and uniform shapes cost-effectively for large production volumes.
Isostatic Pressing: Here, the ferrite magnet material is placed in a flexible mold before being subjected to pressure. The pressure is by a pressurized fluid in a uniform and multidirectional manner. This forms a green compact with a near-isostatic distribution of stress capable of complex shapes.
Wet Pressing: This is typically done at between 5-15 MPa in the presence of a strong magnetic field perpendicular to the pressing direction. A slurry of the magnet material is made with the addition of a binder to enhance compression. Using plaster or silicone rubber molds treated with release agents prevents sticking. Detailed designs with intricate shapes can be achieved via this process.
Extrusion: Here, the magnetic material is forced through a die of a given shape from which it emerges as a continuous piece. This method is utilized for making magnets with particular cross-sectional shapes like tubes, rods, or custom shapes.
Sintering
The densification process in sintering helps in the achievement of the desired magnetic properties. In this process, temperature and time are critical factors, the former typically ranging between 1200°C to 1300°C. Sintering time will depend on factors like material composition and equipment used.
It is characteristic to use a controlled atmosphere when undertaking sintering to prevent oxidation and undesirable chemical reactions. Gases such as hydrogen, atmospheric air, or nitrogen can be used.
A cooling process typically succeeds the sintering process upon attaining the intended sintering temperature and time. The cooling process is controlled to prevent thermal shock and cracking where the temperature is reduced to room temperature.
Machining and Finishing
Applying surface finishing improves the appearance of the magnet, functionality and surface quality. It can include processes like abrasive blasting, polishing, sanding and lapping that help achieve specific surface texture. The method of choice depends on the desired finish and material characteristics.
Some applications may require the magnets to have protective coatings for corrosion prevention and enhanced resistance to wear. Such coatings include gold and nickel plating, and epoxy.
Magnetizing
Typically, ferrite magnets are manufactured in a demagnetized state preventing unintended magnetization during the process. The magnetizing equipment includes electromagnets, which generate a strong magnetic field upon the passage of electric current through a coil.
Pulsed magnetizers can also be utilized where strong magnetic fields are generated by brief, high-intensity current pulses. These are especially used when undertaking high-performance magnetization. In both instances, you can control the strength and polarity of the generated field.
When carrying out the magnetizing process, position the ferrite magnet material in the electromagnet or magnetizing fixture in the desired orientation. Polarity is determined by the applied magnetic field’s direction during magnetization.
Grades of Ferrite Magnets
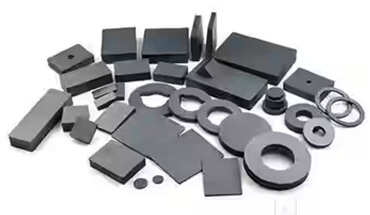
Anisotropic Grades
These have been magnetized in a specific direction and display higher magnetic performance. Anisotropic ferrite magnets are used in applications requiring a specific magnetic orientation. They include Y30, Y32, Y33, Y35 and Y36.
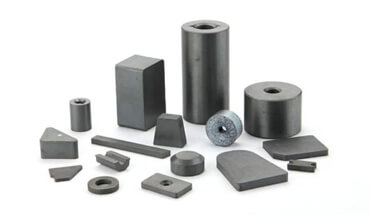
High Temperature Grades
These ferrite magnets are particularly developed to thrive in high-temperature environments. They can withstand temperatures up to 350°C whilst maintaining their magnetic properties.
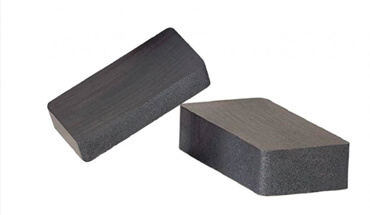
Isotropic Grades
These ferrite magnets lack a preferred direction of magnetization. They exhibit similar magnetic properties in all directions and include Y8T, Y10T,Y30H-1 and Y34.
Properties of Ferrite Magnets
Ferrite magnets have a few identifiable properties that allow their specific use in certain applications. These properties derive from their manufacturing process, inherent structure, and composition.
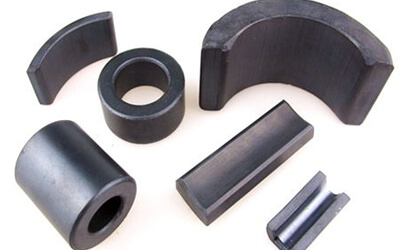
Magnetic Strength
Coercivity (Hc)
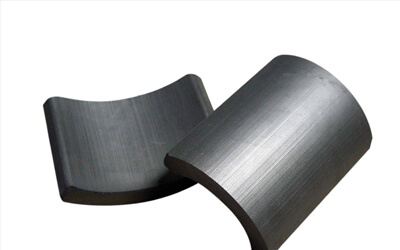
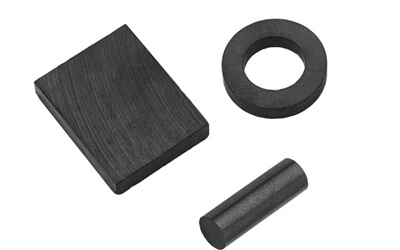
Magnetic Permeability (μ)
This fundamental property characterizes the ease with which a material can obtain magnetic properties when placed within an external magnetic field. The magnetic permeability of ferrite magnets is high when in the presence of low to moderate magnetic fields.
This property allows their use in electromagnetic field manipulation and energy transfer applications like in inductors and transformers. In the former, they work well in electromagnetic devices where they concentrate magnetic flux lines.
Temperature Stability
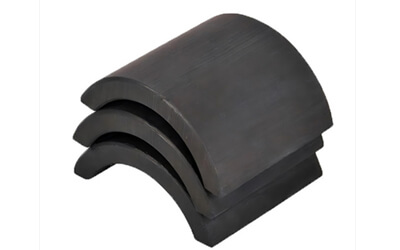
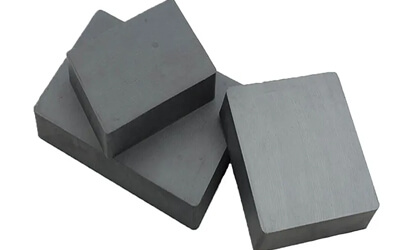
Electrical Insulation
Low Density
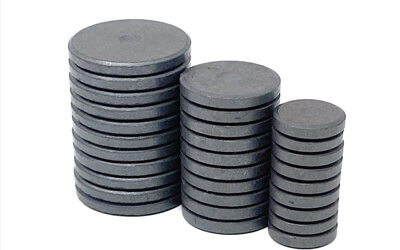
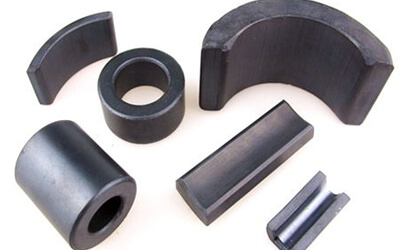
Magnetic Orientation
Uses of Ferrite Magnets
Electrical Motors
Brushless DC motors that use ferrite magnets to induce a magnetic field whose interaction with the rotor’s electromagnets results in motion.
Household appliances like refrigerators, washing machines and air conditioning units utilize these magnet in motors to provide efficient motion.
Automotive motors like those that power cooling fans and control windshield wiper motors utilize ferrite magnets
. Ferrite magnets find use in power tools such as handheld grinders and cordless drills to induce the required magnetic field.
Office equipment like copiers and printers incorporate ferrite magnet-based motors for their moving parts.
Speakers and Audio Equipment
In loudspeakers, these magnets are attached to the diaphragm where their magnet field interacts with electrical current to create sound waves.
Headphones and earphones utilize ferrite magnet-based drivers in the conversion of electrical signals into sound.
Audio systems like amplifiers utilize these magnets in their transformers and other electromagnetic parts.
In some musical instruments like electric guitars and keyboards, ferrite magnets spearhead the conversion of musical input into electrical signals.
Many car audio systems constitute ferrite magnet drivers in their configuration for in-car sound and entertainment.
Magnetic Closures
Ferrite magnets are used to secure wearable jewelry pieces like necklaces and bracelets, providing just enough force to hold them together.
Ferrite magnets are utilized in doors and cabinets like those used in kitchens to provide a convenient way of securing them.
Ferrite magnets are utilized in electronic device cases such as laptops, smartphones, and tablets offering a magnetic system of closing and opening.
Magnetic closures in wallets, bags, and purses use embedded ferrite magnets to provide a simple way of opening and closing them.
Magnetic closures using ferrite magnets can be used for boxes and other packaging to provide an opening and closing mechanism.
Some notebooks, book covers and binders use ferrite magnet closures that reliably keep them closed.
Sensors and Actuators
Automotive and industrial applications like machine monitoring utilize speed sensors that detect the rotating speed of machinery.
Hall-effect sensors utilizing ferrite magnets find use in the detection of current flow, position, and speed. They measure conductor voltage when in the presence of a magnetic field.
In proximity sensors, they detect the presence of nearby objects where interaction with the magnetic field induces an output change.
Magnetic encoders fashioned using ferrite magnets convert linear or rotary motion into electrical signals finding use in robotics and motor control.
Magnetic switches utilize ferrite magnets to generate a magnetic field used in security systems and automotive controls to turn on or off.
These magnets are also found in field sensors commonly used in navigation systems to measure magnetic field strength and direction.
Electromagnetic relays utilize ferrite magnets to control the opening and closing of electrical circuits via magnetic field interaction.
Medical Devices
Ferrite magnets can be used to make closures for removable dental artifacts like retainers and dentures.
Gradient coils in MRI machines utilize ferrite magnets to generate spatial magnetic field variations useful in image encoding.
Latching mechanisms used for some medical equipment use ferrite magnets.
Medical sensors requiring moderate magnetic fields can implement ferrite magnets.
Therapeutic devices that utilize magnetic fields such as therapy mats can incorporate ferrite magnets for body relaxation and pain relief.
Automotive Applications
Analog odometers and speedometers utilize ferrite magnets to move the magnetized needle by generating a magnetic field.
Electric window motors utilize ferrite magnets to initiate up and down movement.
Ferrite magnets power the windshield wiper motors to generate a magnetic field behind the wiper blades motion.
Automotive cooling systems can depend on ferrite magnets for the creation of the magnetic field that powers the blades.
When used in ABS sensors, ferrite magnets generate the magnetic field whose interaction with the encoder disks/toothed rings regulates wheel speed.